|
Chapter 6:
Cost Accounting |
Contents:
Chapter 6: Cost Accounting
6.1 Accounting for Manufacturing
Operations
6.2 Product Costs vs. Period Costs
6.3 Product Costs and the Matching
Principle
6.4 Cash Effects
6.5 Inventories of a Manufacturing
Business
6.6
You as the Chief
Financial Officer
6.7
The Need for "Per
Unit Cost Data"
6.8
Determining the Cost
of Finished Goods Manufactured
6.9
Financial Statements
of a Manufacturing Company
|
|
|
6.1
Accounting for Manufacturing Operations
 |
6.1 Accounting
for Manufacturing Operations
A
Merchandising company buys its inventory in a ready-to-sell
condition. Therefore,
its cost of goods is mostly composed of the purchase price
of the products it sells. A manufacturing company, however,
produces the goods that it sells. As a consequence, its cost
of goods sold consists of various manufacturing costs,
including the cost of materials, wages earned by production
workers and a variety of other costs relating to the
operation of a production facility.
Manufacturing
operations are an
excellent example of how managerial and financial accounting
overlaps because manufacturing costs are of vital importance
to both financial and managerial accountants also rely on
prompt and reliable information about manufacturing costs to
help answer such questions as:
What sales
price must we charge for our products to earn a reasonable
profit?
Is it possible
to lower the cost of producing a particular product line in
order to be more prices competitive?
Is it less
expensive to buy certain parts used in our products than to
manufacture these parts ourselves?
Should we
automate our production process with a robotic assembly
line?
|
Classifications of Manufacturing Costs
Direct materials
Direct labor
Manufacturing overhead |
6.1.1 Classifications of Manufacturing Costs
A typical
manufacturing company purchases raw materials and converts
these materials into finished goods through the process of
production. The conversion from raw materials to finished
goods results from utilizing a combination of labor and
machinery. Thus manufacturing costs are often divided into
three broad categories:
(a) Direct materials the raw
materials and component parts used in production whose costs
are directly traceable to the products manufactured.
(b) Direct labor - Wages and
other payroll costs of employees whose efforts are directly
traceable to the products they manufacture, either by hand
or with machinery.
(c) Manufacturing overhead a
catch all classification, which includes all manufacturing
costs other than the costs of direct materials and direct
labor.
Examples include factory utilities,
supervisor salaries, equipment repairs and depreciation on
machinery.
Note that
manufacturing costs are not immediately recorded as current
period expenses. Rather.
They are costs of creating inventory and they remain on the
balance sheet until the inventory is sold. For this reason
manufacturing costs are often calls product costs (or
inventorial costs).
|
6.2
Product Costs
vs. Period Costs
Operating expenses
Distinction between product and period costs

|
6.2 Product
Costs vs. Period Costs
The terms
product costs and a period costs are helpful in explaining
the difference between manufacturing costs and operating
expenses. In a
manufacturing environment, product costs are those costs
incurred to manufacture inventory. Thus, until the related
goods are sold, Product costs represent inventory. As such,
they are reported on the balance sheet as an asset. When the
goods are ultimately sold, product costs are transferred
from the balance sheet to the income statement. Where they
are deducted from revenue as the cost of goods sold
Operating
expenses that are
associated with time period, rater than with the production
of inventory, are referred to as period costs. Period costs
are charged directly to expense accounts on the assumption
that their benefit is recognized entirely in the period when
the cost is incurred. Period costs include all selling
expense, general and administrative expenses, interest
expense, and income tax expense. In short period costs are
classified on the income statement separately from cost of
goods sold. As deductions from a company's gross profit.
The flow of
product costs and period costs through the financial
statements is shown in the diagram below.
To further
illustrate of the distinction between product and period
costs, consider two costs that, on the surface, appear
quite similar: the depreciation of a warehouse used to store
raw materials versus depreciation of a warehouse used to
store finished goods. Depreciation of the raw materials
warehouse is considered a product cost (a component of
manufacturing overhead) because the building is part of the
manufacturing process. Once the manufacturing process is
complete and the finished goods are available fro sale all
costs associated with their storage are considered selling
expenses. Thus the depreciation of the finished goods
warehouse is a period cost.
|
6.3
Product Costs and the Matching
Principle
Example
|
6.3 Product
Costs and the Matching Principle
Underlying
the distinction between product costs and period costs
is familiar accounting concept the matching principled. In
short, Product costs should be reported on the income
statement only when they can be matched against product
revenue, to illustrate see Table 6.1:
Table 6.1: Product costs
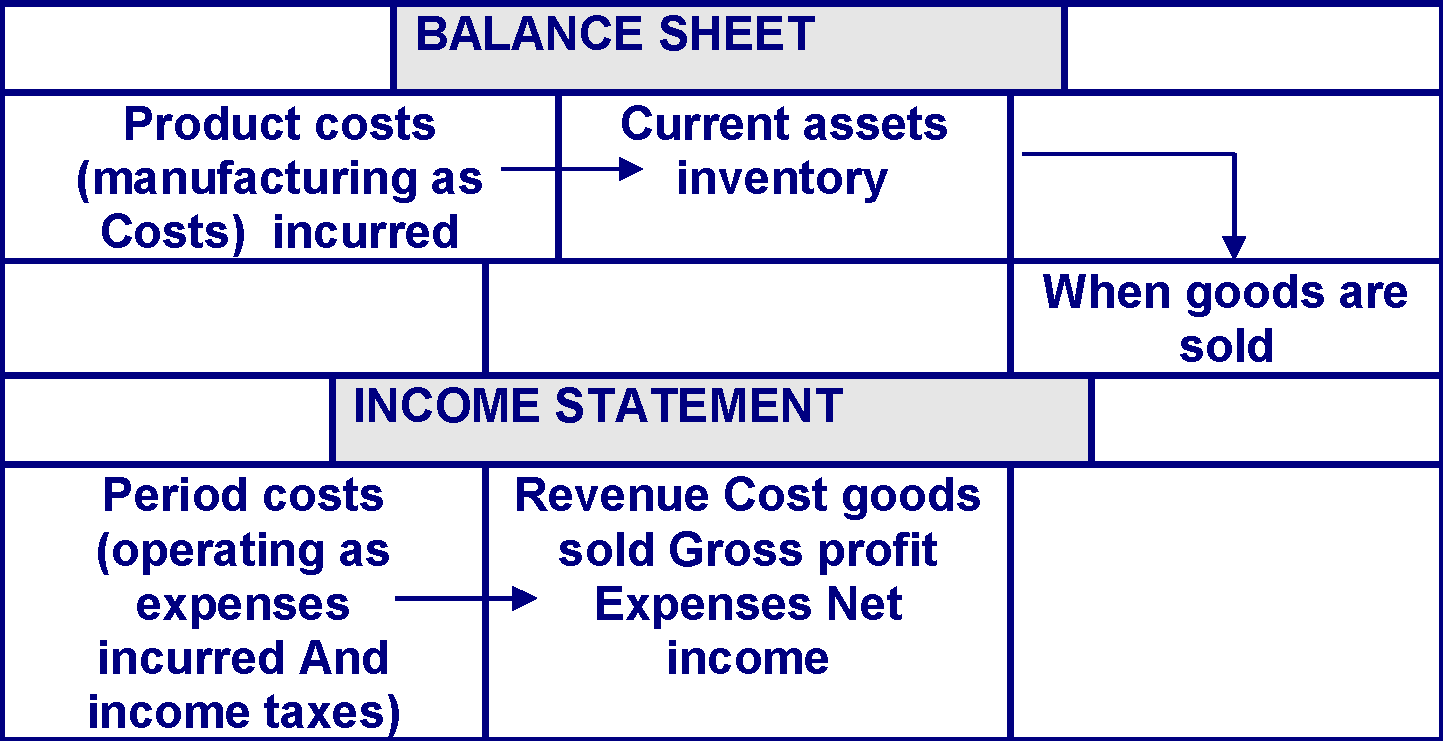
Consider a
real estate developer who stats a tract of 10 homes in May
of the current year,
during the year, the developer incurs material, labor, and
overhead cost amounting to $ 1 million ( assume $ 100,000
per house ) . By the end of December, none of the houses has
been sold. How much of the $1 million in construction costs
should appear on the developer's income statement for the
current year?
The
answer is none. These costs are not related to any revenue
earned by the developer during the current year.
Instead, they are related to future revenues the developer
will earn when the houses are eventually sold. Therefore, at
the end of the current year, the $ 1 million of product
costs should appear in the developer's balance sheet as
inventory. As each house is sold $ 100,000 will be
deducted from sales revenue as cost of goods sold. This way,
the developer's income statements in future period will
properly match sales revenue with the cost of each sale.
|
6.4
Cash Effects
 |
6.4 Cash Effects
Classifying costs as
period or product costs can have significant cash
effects when the classification determines in what period
the cost appears on the income statement as an expense.
Using the real estate developer example above, assume the $1
million in construction cost was classified as a period
expense rather than a product expense. The current period's
net income would be substantially reduced by the additional
$1 million in expenses and the cash flow associated with the
current year's income taxes would be significantly
reduced.
|
6.5
Inventories of a Manufacturing
Business
In many countries
|
6.5 Inventories
of a Manufacturing Business
In the
preceding example,
assume all 10 houses were completed by the end of the year;
in this case the developer's inventory consists only of
finished goods. Most manufacturing companies, however
typically account for three of inventory.
Materials
inventory raw
materials on hand and available for use in the manufacturing
process.
Work
in process inventory
partiality completed good on which production activities
have been started but not yet completed.
Finished
good inventory unsold
finished products available for sale to customers. All three
of these inventories are classified on the balance sheet as
current assets. The cost of the materials inventory is based
on its purchase price. The work in process and finished
goods inventories are based on the costs of direct martial.
Direct labor and manufacturing overhead assigned to them.
In
many countries such as Argentina and Greece, inventory
valuation does not conform to the lower of cost or market
value rules used in the united stated.
In addition, many countries, including Brazil, Korea,
Mexico Nigeria, Poland, and Taiwan allow upward revaluation
of property and equipment; these differences in
accounting methods make comparing inventory values of
companies from different parts of the world very difficult.
Manufacturing
companies may use either
a perpetual or a periodic inventory system. Perpetual
systems have many advantages, however, such as providing
managers with up to date information about the amounts of
inventory on hand and the per unit costs of manufacturing
products. For these reasons, virtually all large
manufacturing companies use perpetually inventory systems.
Also the flow of manufacturing costs through the inventory
accounts and into the cost of goods sold is most easily
illustrated in a perpetual inventory system. Therefore, we
will assume the use of a perpetual inventory system, in our
discussion of manufacturing activities.
|
6.6
You as the Chief
Financial Officer
 |
6.6
You as the Chief
Financial Officer
Assume that you are
the chief financial officer of Conquest, Inc., and that you
have just received an income statement and balance sheet from
plant accountant Jim Sway in Bend, Oregon. In your
conversations with Jim you learn that in the recent reporting
period, plant manager Darien Cocky asked that inventory
transportation cost, the cost of repairing the plant parking
lot, and the newly installed plant landscaping costs all be
allocated to the cost of production. In addition, when these
allocations took place, the plant produced many more bicycles
than were sold creating significant increased in the amount of
inventory on hand. As a result, most of the costs described by
Jim have been assigned to the inventory,) (included as part of
inventory costs on the balance sheet), but have not been
assigned to cost of goods sold expenses (Included on the income
statement).
|
6.7
The Need for "Per
Unit Cost Data" |
6.7
The Need for "Per
Unit Cost Data"
Transferring the
cost of specific units from one account to another requires
knowledge of each unit's per unit cost
that is the total manufacturing costs assigned to specific
units. The determination of unit cost is one for the primary
goals of every cost accounting system.
Unit
costs are of importance to both financial and management
accountings. Financial
accountants use unit costs in recording the transfer of
completed goods from work in process to finished goods and from
finished goods to cost of goods sold management accountants use
the same information to make pricing decisions. Evaluate the
efficiency current operations, and plan for future operations.
|
6.8
Determining the Cost
of Finished Goods Manufactured

|
6.8
Determining the Cost
of Finished Goods Manufactured
Most
manufacturing companies prepare a schedule of the cost of
finished gods manufactured to provide mangers with an overview
of manufacturing activities during the period.
Schedule of Summit cost of finished goods manufactured is shown
in Table 6.2.
Summit Inc.
Schedule of the cost of finished goods manufactured
For the year ended December 31, 2004 |
Work in process
inventory , beginning of the year |
|
$ 30,000 |
Manufacturing cost
assigned to production |
|
|
Direct materials used
|
$150.000 |
|
Direct labor
|
$300,000 |
|
Manufacturing overhead |
$360,000 |
|
Total manufacturing
costs |
|
$810.000 |
Total cost of all work
in process during the year |
|
$840,000 |
Les : work in process
inventory end of the year |
|
(40,000) |
Cost of finished goods
manufactured |
|
$800.000 |
A schedule of the
cost of finished goods manufactured is not a formal financial
statement and generally does not appear in the company's annual
report. Rather, it is
intended primarily to assist mangers in understanding and
evaluating the overall cost of manufacturing products by
comparing these schedules for successive periods, for example,
managers can determine whether direct labor or manufacturing
overheads is rising or falling as a percentage of total
manufacturing costs. In addition, the schedule is helpful in
developing information about unit costs.
If a company
manufactures only single product line, its cost per unit simply
equals its cost, if finished goods manufactured divided by the
number of units produced. For example if Summit produces only
one line of mountain bike, its average cost per unit would be
$80 had it produced 10,000 finished units during 202 ($800,000
divided by 10.000 units) If conquest produced multiple lines of
mountain bikes, it would prepare a separate schedule of the cost
of finished goods manufactured for each product line.
|
6.9
Financial Statements
of a Manufacturing Company |
6.9
Financial Statements
of a Manufacturing Company
Let us now
illustrate how the information used in our example will be
reported in the 2004 income statement and balance sheet of
Summit Inc. The company's
2004 income statement is presented in Table 6.3:
Table 6.3:
Income statement of
Summit Inc.
Summit Inc.
Income statement
For the year ended December 31, 2004 |
Sales |
|
$1,300,000 |
Cost of goods sold |
|
$ 782,000 |
Gross profit on sales
|
|
$ 518,000 |
Operating expenses
|
|
|
Selling expenses
|
$135,000 |
|
General and
administrative expenses |
$265,000 |
|
Total operating expenses |
|
$400,000 |
Income from operations
|
|
$ 18,000 |
Less : interest expense
|
|
$ 18,000 |
Income before income e
taxes |
|
$ 30,000 |
Net income
|
|
$ 70.000 |
Notice that no
manufacturing costs appear among the companys operating
expenses. In fact,
manufacturing costs appear in only two places in a
manufacturer's financial statements. Costs associated with units
sold during the period appear in the income statement as the
cost of goods sold. The $782,000 cost of goods sold figure
reported in Summit's income statement was taken directly forms
the company's perpetual inventory records. However, this amount
may be verified as shown in Table 6.4:
Table 6.4: Income
statement
Beginning finished goods
inventory (1/1/04) |
|
$150,000 |
Add: cost of finished
goods manufactured during the year
|
|
$800,000 |
Cost of finished goods
available for sate |
|
$950,000 |
Less : Ending finished
goods inventory (12/31/04) |
|
$168,000 |
Cost of goods sold
|
|
$782,000 |
Summit Inc.
Partial balance sheet (December 31,
2004) |
Current assets : |
|
|
Cash and cash
equivalents |
|
$60,000 |
Accounts receivable (
net of allowance for doubtful accounts
|
|
$190,000 |
Inventories : |
|
|
Materials
|
$20,000 |
|
| | | | |