2.1 Total
Safety Management Definition
Total safety management is a performance-oriented approach
to safety and health management that gives organizations a
sustainable competitive advantage in global marketplace by
establishing a safe and health work environment that is
conducive to consistent peak performance and that is improved
continually forever.
This definition contains several key elements that must be
understood if one is to fully understand TSM. These elements are
as follow:
2.1.1 Sustainable competitive advantage
Every organization that competes at any level, but
especially those that compete at the global level must have
competitive advantages. These are capabilities or
characteristics that allow them to outperform the competition. For example, if the organization in question is a baseball
team, it might have such competitive advantages as an excellent
pitching staff, several speedy base runners, two or three power
hitters and/or outstanding fielders in key positions. These
advantages, if exploited wisely, will help make the baseball
team a winner. If these advantages can be sustained over time,
they will help make team a consistent winner.
This same concept applies to
organizations that compete in the global marketplace. In
order to survive and proper, they need as many competitive
advantages as possible. Traditionally, competitive advantages
have been sought in the key of quality, productive, service, and
distribution. However, peak-performing organization has learned
that a safe and healthy work environment is essential to gaining
competitive advantages in these critical areas. In fact, a safe
and healthy work environment is itself a competitive advantage.
|
|
2.2 Peak
Performance
The primary driver behind TSM is organizational,
team, and individual performance. An organization's ability to survive and proper
in the global marketplace is determined largely by the
collective performance of individuals and teams. Consistent peak
performance by all individual and teams in an organization is
essential to long-term success in the global marketplace. The
quality of the work environment is a major determinant of the
performance levels that individuals, teams and organizations are
able to achieve. A better work environment promotes better
performance. |
|
2.3
Continual Improvement Forever
People work in an environment, and the quality of that
environment affects the quality of work. The work environment is
a major determinant of the quality of an organization's
products, and services. In the age of global competition,
quality is an ever-changing phenomenon. A quality that is
competitive today may not be tomorrow. Consequently, continual
improvement is essential. If quality must be improved
continually, it follows that the work environment must also be
improved continually.
|
|
2.4
Translating TSM into Action
There are three fundamental components through which the TSM
philosophy is translated into action on a daily basis. These
three components are the TSM steering Committee, Improvement
Project Teams (IPTs) and the TSM Facilitator.
The TSM Steering Committee oversees the organization's safety
and health program. It is responsible for formulation of safety
and health policies, the approval of internal regulations and
work procedures relating to safety and health, the allocation of
resources, and approval of recommendations made by the IPTs.
|
|
2.5
Implementing TSM: the Model
Figure 2.1 contains a three-phase fifteen-step model that can
be used for successfully implementing TSM in any organization.
Steps in the TSM implementation process |
Planning and preparation
-
Gain Executive-Level Commitment
-
Establish the TSM Steering Committee
-
Mold the steering committee into Team
-
Give the Steering Committee Safety and Health
Awareness Training
-
Develop the organization's Safety and Health
Vision and Guiding Principles
-
The organization's Safety and Health Mission and
Objectives
-
Communicate and Inform
-
Identification and Assessment
-
Identify the Organization's Safety and Health
Strengths and Weaknesses.
-
Identify Safety and Health Advocates and
Resisters.
-
Benchmark Initial Employee Perceptions
Concerning The Work Environment.
-
Tailor Implementation to the organization.
-
Identify Specific Improvement Projects.
-
Establish, Train, and Activate Improvement
Project Teams
Execution
-
Activate the Feedback Loop
-
Establish a TSM Culture
|
Figure 2.1: Model for implementation |
|
2.6
Executive Commitment – A Must
In
any organization, the aim and direction are decided by the chief
executive officer (CEO) and the members of his or her executive
management team. These individuals decide what will be
emphasized where limited resources will be spent, what behavior
will be rewarded and what won't, and how incentives will be
used. Mid-managers and supervisors take their cues from
executive mangers. They, in turn, pass perception along to
employees.
The
TSM philosophy requires that the total organization be involved
continually improving the work environment. TSM cannot be
implemented in just one department or by just a few employees.
By definition, such an approach would not be total safety
management, and anything short of total environment robs the
organization of the full benefits of TSM.
Consider just a few of the things that must be done in order for
TSM to be implemented:
·
Safety and health must be included
as high priority concerns in the organization's strategic
plan.
·
Resources must be allocated to cover implementation costs. Employee performance relative
to safety and health must be monitored, evaluated, and rewarded
as appropriate.
·
Safety and health must be monitored, evaluated,
and rewarded as appropriate.
·
Employees must be shown that safety is a must
no matter how pressed the organization becomes to meet deadlines
·
Who but the CEO and executive managers of the
organization has the authority to do these things? The answer is no one.
Consequently, executive commitment is a must.
|
|
2.7
Achieving Executive Commitment
What does it mean to achieve executive commitment? The concept is defined by its three components as
shown in Figure 2.2. Any other concept for that matter will be
personally involved in its implementation.
Figure 2.2: Components of executive commitment
|
Personal
Involvement |
|
+
|
|
Commitment
of Time |
|
+
|
|
Commitment
of Resources |
|
|
=
|
Executive
Commitment |
Figure 2.3 contains a checklist of ways in which an
executive–level manager can be personally involved in TSM.
An executive manager
who is completely committed to TSM will want to serve on the
organization's TSM steering Committee. The ideal steering
committee consists of the organization's executive managers, or
if the CEO and his/her executive managers do not serve on the
TSM Steering Committee, they will have to go to even greater
lengths to demonstrate their commitment to safety health.
Otherwise the committee's credibility will suffer.
Figure 2.3: TSM personal – involvement
checklist for executive- level mangers
 |
Serving as a member of the organization's TSM
Steering |
 |
Advocating for inclusion of safety and health
concerns in the organization's strategic plan.
|
 |
Personally giving improvement project teams (IPTs)
their charges |
 |
Participating in training activities as appropriate
, |
 |
Maintaining a high profile in and supportive
attitude toward all TSM activities |
|
|
2.8 Total
Safety System Implementation Case Study
Healthy Food
is moving the company forward in implementing TSM, but it isn't
sure what the process will mean for its executive management
team. It is knows that each member of the team will have to be
personally involved in the implementation, but what does
personally involved really mean? The company wants to know as
do Health Food's other executive mangers. If you are Company's
TSM Facilitator. How would you explain personal involvement to
Mary Earnst?
The safety and health manager for the organization meets with
the executive management team whenever it sits as the TSM
Steering Committee, and serves, in such cases as the committee's
facilitator and consultant.
Executive managers committed
to TSM will advocate on behalf of health and safety health when
developing the organization's strategic plan. Through their
involvement in the process, executives can ensure that safety
and health concerns show up in the organization's strategic plan
guiding principles and/or broad objectives, or both.
Each time an Improvement Project Team (IPT) is established to
deal with a specific safety or health concern, executive
managers can be personally involved by giving the team its
charter.
Receiving its charter directly from the CEO or another executive
manager tells IPT that the activity in question is important.
Personal participation in the various training activities
associated with implementing TSM is doubly beneficial for
executive managers.
First executives learn what they need to know in
order to play a positive role in rendering the TSM philosophy
operational. |
|
2.9
Evaluation of Executive Comment
Executive Commitment to TSM- with rare exceptions- will take
time to achieve.
Safety and health managers should expect to confront the
evolutionary steps shown in Figure 2.4. Executive mangers may be
skeptical when they first hear about TSM as normal human
response to change, and TSM means change. A persuasive argument,
persistent but patiently repeated often enough, may move
executive managers to the next level: tentative. If so, the
safety and health manager will probably be asked to make a
presentation to the executive management team. If presentation
goes well, TSM will probably be provisionally accepted.
At
this point, it's a good idea to undertake pilot project to
demonstrate how TSM can make a difference. For example, an
IPT might be formed to confront a specific safety/health
problem. If the pilot goes well, executive managers will
probably move to the buy-in stage. Once TSM has been implemented
widely and positive results have been demonstrated, executives
will probably move to the commitment phase.
Figure 2.4: Evolution of commitment
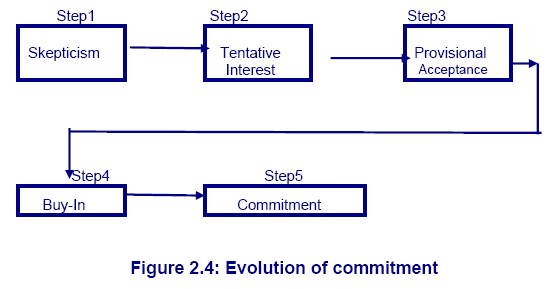 |
|
2.10
Four-Steps for Gaining Executive Commitment
In
order to gain executive commitment, the safety and health
manager must show that TSM is good business. Figure 2.5 shows a
four- step process that can be used to make this point. The
following sections expand on steps.
2.10.1
Preparation
Preparation involves conducting the research necessary to answer
questions such as those shown in the figures. Notice that only
one question in Figure 2.5 deals with regulatory compliance, and
this question is cast economic, not compliance terms. TSM will
ensure regulatory compliance, but this is a secondary, not a
primary benefit.
Figure 2.5: Process gaining effective commitment
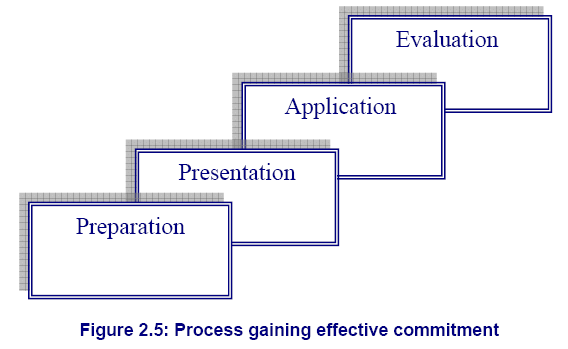
2.10.2 Presentation
Once
the research step has been completed, the next step involves
presenting findings to executive management. The presentation
consists of answering types of questions shown in Figure 2.6. An
effective approach is to use visual aids.
2.10.3 Application and Evaluation
The
purpose of the previous step (presentation) was to create enough
executive buy-in to allow the TSM implementation to proceed.
Full commitment is not likely to occur until executive
management has the concept successfully applied. Consequently,
it is important at this point to accomplish the following tasks:
·
Convince executive management to commit to give
TSM their full support long enough to allow for positive
results.
·
Clearly define success
and decide how it will be measured. It is important for
everyone involved in the implementation of TSM to understand
what is exacted, what they will be held accountable for, how
progress will be assessed, and how performance will be
evaluated.
2.10.4 Maintaining Executive Commitment
Initial excitement followed by flagging interest is a common
phenomenon when implementing a new concept, particularly when
that concept represents major cultural change. Management
executive commitment, long enough to allow TSM to break the
bonds of cultural inertia and become, itself the cultural norm
is a challenge. Figure 2.7 is the plan-do-check–adjust (PDCA)
cycle superimposed on a blanket of continual compunction.
1.
|
Is this company's performance in the marketplace as
good as we would like it to be? |
2.
|
Does this company have any sustainable competitive
advantages over its competitors? If so what are
they? |
3.
|
Is this company spending more than it should on
workers' compensation costs? Are works' compensation
costs in this company increasing, decreasing or
remaining stable? |
4.
|
Are the company's insurance premiums acceptable? Are
the premiums increasing, decreasing or remaining
stable? |
5.
|
Is product quality as good as we would like it to
be? |
6.
|
Is product price consistently below that of
competitors? |
7.
|
Is productivity in this company as high as we would
like it to be? |
8.
|
Is the number of hours lost due to accidents in this
company as low as we would like it to be?
|
9.
|
Is the absenteeism rate in this company as low as we
would like it to be? Is the rate increasing,
decreasing or remaining stable? |
10.
|
Is the sick leave utilization rate in this company
low we would like it to be? Is the rate increasing,
decreasing or remaining stable? |
11.
|
How frequently is this company involved in
safety/health related litigation? How much is spent
annually on this type of litigation? Is the amount
spent on safety/health litigation increasing,
decreasing, or remaining stable? |
12.
|
Is employee morale at this company as we would like
it to be? |
13.
|
Is the employee turnover rate at this company
acceptable? Is it increasing, decreasing, or
remaining stable? |
14.
|
Do employees perceive the work environment in this
company as a positive or negative factor?
|
15.
` |
Has this company been required regulatory agencies
to pay safety/health related fines? If so, in what
amounts? |
Figure 2.6: Question for gaining executive commitment to TSM
Figure 2.7
is a checklist of tips that will help enhance the quality and
effectiveness of presentation made to effective managers.
These are tips that apply to presentations made to small groups-
between five and fifteen people – in a conference room or
similar setting.
·
|
Keep the presentation brief and to the point.
Executives are busy people. |
·
|
Base the presentation on documented facts. Never
make claims you cannot support. |
·
|
Use well-designed, attractive visual aids. Keep
visual aids simple and make sure all information on
them can be easily seen from the back of the room.
|
·
|
Do at least two complete trial runes (practice
sessions) before making the presentation. During the
actual presentation is no time to be working out the
bugs. |
·
|
Arrive early and set up. Test all equipment and have
back-up strategies in case something malfunctions
during the presentation |
·
|
Make sure presentation has three distinct
components: introduction, Body, and Summary.
|
·
|
If you nervous, concentrate on slowing down your
rate of speech. Nervous speakers are prone to rust
|
·
|
Make eye contact with all members of the audience,
and speed your attention equally. People don't like
to be ignored. |
Figure 2.7: Presentation tips for safety and health mangers
2.10.5 Structure of Periodic Progress Reports
Periodic progress reports given to executive managers should
pick up where the presentation made to win their initial
commitment left off.
The same criteria used to gain executive commitment should be
used for maintaining it. If, for example, lost time due to
accidents was criterion in the commitment presentation, it
should be a criterion in the progress reports. Has the amount of
lost time declined? If so is, by how much?
The
need for continuity between the criteria used to gain commitment
and that used to maintain it underscores the importance of
basing the commitment presentation on documented facts. The
safety and health manager who overstates during the commitment
presentation will pay for it when making periodic progress
reports. This can be a sure way to lose commitment. |
|
2.11 The
Safety Management Function
The concept of safety management began when a
better description than safety engineer was needed for the work
of the safety specialist. Whether an engineer or not, he or she is concerned largely with
convincing others to follow applicable safety requirements.
There are notable differences usually between managing as
carried out by the head of an operating unit and that which is
noted in a safety management position. Managers of units
accomplishing the prime purposes of an organization have direct
authority over the personnel in their unit. Safety management,
however, is conducted generally as a staff assignment. The
director or chief of safety has managerial authority over the
professional personnel reporting directly to him or her, but the
powers of line managers are not to be transmitted through the
safety specialists. |
|
2.12
Safety and Plant Size
It has been widely believed that small plants represent the
greater occupational safety and health problem. To be sure,
they are far more numerous than locations with large numbers of
employees, Table 2.1. And injury records show that generally the
very large plants with more than 2,000 employees tend to have
much better injury experience than smaller ones, particularly
those in the 50 to 500 size range.
Table 2.1: Injury frequency rate related to number of employees
Reporting Units
(number employed |
Injury
Frequency Rate |
Less than 20 |
9.9 |
20 to 49 |
13.4 |
50 to 99 |
17.0 |
100 to 249 |
21.4 |
250 to 499 |
17.9 |
500 to 999 |
14.2 |
1.000 to 2.4 |
11.2 |
2.5 or more |
7.3 |
|
|
2.13
Safety Management Propositions
Five safety management propositions emerge.
The first three are addressed essentially to higher management
in general, with numbers four and five to be carried out by the
safety staff.
a.
Keep separate and visible the lines
responsibilities for safety from the staffs.
b.
Hold the line clearly accountable
for the operation's safety effectiveness.
c.
Hold the safety staff accountable
for the correctness and persuasiveness of the information it
provides line management.
d.
Develop operating objectives
for safety with management's needs and goals, while leading to
the fulfillment of establishment safety requirements.
e.
Measure hazard control effectiveness
on bases which conform to management's appraisals of its
performance. |
|
2.14
Analysis of the Propositions
A
and B are separating line responsibility for safety from
staff often has been easier to discuss than to accomplish.
The principle is clear. On one side is the power line of
authority, on the other is the authority of knowledge that
competent specialists acquire.
C
The accountability of the safety staff is complicated,
but not difficult to define. Staff positions in general fall
into one or two types, advisory and/or assisting or performance
of a specialized function for the total organization to
facilitate the operation of the line departments.
D
Operating objectives that fulfill safety requirements
and parallel management goods in effect energize the hazard –
control mechanism. It cannot be assumed that safety requirements
will be compiled with simply because they are called for.
Therefore, means must be found which at least will harness the
power of the hierarchy in mounting the attack on hazards. This
is a reason, of course, for safety laws and regulations. They
are expected to furnish the unambiguous motivation for safety
needed for its fulfillment – as well as to specify the required
controls. If the strength of the organization can be engaged for
safety – health achievement, then compliance can be more
reasonably assured. This may be assumed since the purpose of the
organization is to marshal the abilities of its members in the
pursuit of its mission. An institution's regulation of hazards,
as with the accomplishment of its other requirements, must rely
on the potency of its organization and management.
E
Measurements of hazard–control effectiveness must
be developed and presented in such a way that they are
understood and appreciated by upper levels of management. They
must be such that they provide some compelling interest and
afford the opportunity for appraising management performance. |
|
2.15
Definition of Terms Applicable to Safety Management
Accident:
An event occurring by chance from unknown causes (and therefore
unpreventable)
Hazard:
The source of energy and the physiological and behavioral
factors which, when uncontrolled, lead to harmful occurrences.
Persuasive methods and information: Discipline, required, punishment, and the power of facts well
marshaled when presented in the way necessary to obtain the
desired action.
Risk:
The assumed effect of an uncontrolled hazard, appraised in
terms of the probability it will happen, the maximum severity of
any injuries or damages, and the public's sensitivity to the
occurrence.
Safe:
Protected against hazard.
Safety:
The
elimination of hazard, or their control to levels of acceptable
tolerance as determined by law, and institutional regulations,
ethics, personal requirements, scientific and technological
capability, experiential knowledge, economics, and the
interpretations of cultural and popular practice.
Safety management:
The accomplishment of safety through others.
The work of safety management:
Accomplishing safety by applying persuasive methods and
information in a closed loop system. |
|
|
|
|